Witten by Jeremy Friedmar and Matt Wopata
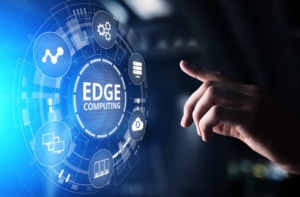
Industrial edge compute devices make edge computing possible. They offer a way to use and gain value from your data, supporting real-time decision making, enhanced security and faster analytical speeds.
In this new and growing market, there’s a plethora of choices. You’ll quickly find that you have several options to consider when searching for industrial edge compute devices.
To make the selection process faster and simpler, we compiled a list of 10 key criteria to consider when selecting an industrial edge compute device.
1. Compute Resources
Industrial edge compute devices have three main types of compute requirements to consider:
- Processor: power (number of cores, performance) and type (ARM vs. x86)
- Memory: quantity (GBs) and type (DDR3, DDR4 or DDR3L)
- Storage: quantity (GBs) and type (SSD vs. eMMC vs. SD card)
It’s vital to match these compute resources with the needs of the applications that will run on them. For instance, analysis equipment may require better processor performance than asset tracking equipment.
This example from industrial software provider Inductive Automation shows compute resource requirements for projects and applications based on their sizes.
2. Form Factor
When it comes to industrial edge compute devices, there are four types of form factors, offering you different choices in size, shape and other physical specifications:
- DIN rail (IP20, IP30 or IP40)
- Panel (on machine, IP67)
- Wall mount
- 19-inch rack
Again, your application will determine the right device size. For example, many small industrial edge compute devices are deployed in DIN rail or panel form factors.
3. Temperature Rating
There are two temperature ratings to consider for your industrial edge compute device:
- Operating temperature: the temperature range of the environment in which the device will operate (steel/glass manufacturers or baked goods production are heat-intensive environments while medical product manufacturing happens in a colder environment)
- Non-operating temperature: the temperature range the device can handle when it’s turned off
Due to the nature of industrial plant environments, industrial edge compute devices often require wider operating temperatures than non-industrial gateways or traditional IT servers. For example, an IT server in an office building doesn’t need to withstand the hot/cold conditions that may be found in a food and beverage processing facility.
You’ll often find common operating temperature ranges like these:
- 5 to 40 degrees C: IT rack servers
- -20 to 60 degrees C: IT gateways
- -40 to 70 degrees C: OT gateways
- -40 to 85 degrees C: extreme environments
4. Power Requirements
What type of power source do you need for your industrial edge compute device? The answer depends on your industry, region, application and what it requires in terms of device temperature, safety, power universality, device size, etc.
Popular input power voltages include:
- 12V DC
- 24V DC
- 36V DC
- 48V DC
- 110/250V DC
- 60/120/260V DC
- 24V AC
- 110/230V AC
You’re most likely to find industrial edge compute devices that support DC voltage ranges from 12V to 48V because industrial panels contain power supplies in that range.
5. Power Distribution
In addition to traditional power supply set-ups, new industrial edge hardware that supports power over Ethernet or power over data line can reduce installation complexity and wiring.
Two popular energy delivery mechanisms are:
- PoDL (power over data line)
- PoE (power over Ethernet)
Power over data line specifies power distribution over a single twisted-pair link segment. It operates in four types:
- Type A: optimized for 10BASE-T1S
- Type B: optimized for 1000BASE-T1
- Type C: optimized for 10BASE-T1S, 100BASE-T1 and 1000BASE-T1
- Type E: optimized for 10BASE-T1L
Power over Ethernet specifies power distribution on twisted-pair Ethernet cabling. It operates in four types as well:
- Type 1: maximum power to port is 15.4W
- Type 2: maximum power to port is 30W
- Type 3: maximum power to port is 80W
- Type 4: maximum power to port is 100W
6. Approvals
Industrial edge compute devices require adherence to safety standards, requirements and approvals that are different than those of non-industrial edge hardware components.
Common approvals for these industrial devices include:
- cUL508/cUL61010-1/-2-201: safety standards for control industrial equipment
- cUL1604/ISA 12.12.01/FM3611: electrical equipment in hazardous locations
- ATEX 100a, Zone 2: hazard location classification
- IEC 61850-3: communication protocols for devices at electrical substations
- IEEE 1613: environmental and testing requirements for communications networking devices in electric power substations
- EN 50155, EN 45545: standards for electronic equipment used on rolling stock for railway applications
- EN 50121-4: standards for signaling and telecommunication apparatus installed in railway environments
Make sure the device you consider adheres to the requirements and standards of your application.
7. Native Networking Interfaces and Features
Industrial edge compute devices often require interfaces to support traditional IT and specific OT applications.
For example, to support IT applications, the devices may feature Ethernet, fiber, Wi-Fi and/or cellular networking interfaces.
To support OT applications, you may see networking interfaces like serial, IO-Link, Single-Pair Ethernet and/or 900 MHz.
Regardless of the networking interfaces integrated into the device, there are certain features you should look for to support data security and accessibility as well:
- Firewalling (e.g., IP whitelisting) that permits or blocks data packets based on pre-set security parameters
- Routing (e.g., LAN to WAN routing, WAN backup, IP masquerading, NAT, port forwarding, L2 bridging) to determine the flow of data transmission
- Remote access/VPNs (e.g., OpenVPN, IPsec, etc.) so people offsite can retrieve the data they need
- Redundancy (e.g., PRP, HSR, RSTP, MRP, DLR, etc.) to align availability and network recovery time with your application
- Protocol support (e.g., EtherNet/IP, Modbus, SNMP, etc.) so the device can interact with different industrial networking protocols
- Networking diagnostics (e.g., .PCAP exports) so you can find the cause of faults in the network
- OT-specific features, including support for the emerging time-sensitive networking (TSN) standard
8. Native Edge Application Management
Modern industrial edge compute devices often come preconfigured with container managers and hypervisors that abstract edge applications from underlying hardware and enable users to seamlessly run virtual machines and containers from a variety of OT edge application vendors.
This feature allows you to manage and deploy workloads.
9. Security
Hardware-based security prevents unapproved code from running on the compute hardware and ensures that your sensitive data is securely stored on the device.
To ensure security, look for features like:
- Secure Boot: a security feature that prevents malicious software from loading so only approved operating systems can boot up
- TPM (trusted platform module): the ability to store security information on the device to improve tamper resistance
10. Non-Technical Considerations
To ensure that you get the most from your investment, there are a few non-technical points to consider for your industrial edge compute device.
First, examine the warranty and end of life (EOL) date. Industrial edge compute devices are expected to survive in the field for many years longer than traditional IT edge compute devices. Make sure the warranties and EOL dates reflect this. To compare typical lifespans:
- OT devices: 5-10 years or longer
- IT devices: 3-5 years max
Next, consider MTBF (mean time between failures), or the average time the device operates between breakdowns. Telcordia SR-332 test results can help predict expected downtime per year and system availability levels so you know what to anticipate.
Finally, take time to get to know the people behind the industrial edge compute device you’re considering. Do they understand your industry and your unique challenges? Can they answer your questions?